Drones have become an essential tool for building inspections, providing efficiency, safety, and high-quality deliverables. This guide covers the pre-flight tasks, inspection methodology, safety considerations, and deliverables, including software and data processing options. High Exposure follows a protocol for all inspections for their clients in and around Sydney as well as across Australia. While each inspection may have it’s own unique challenges, it is necessary to work from a common set of procedures when approaching a new project.

Pre-Flight Tasks
Site Assessment & Planning
- Identify the building’s height, material types, and areas of interest (e.g., cracks, leaks, corrosion).
- Evaluate obstacles such as power lines, trees, or other structures.
- Determine airspace restrictions and obtain necessary licenses and approvals (e.g.CASA issued ReOC and operator RePL as well as specific area authorisations from CASA and local governing bodies).
Equipment Check & Setup
- Drone selection: Use high-resolution camera drones like the DJI Mavic 3 and 4 Enterprise, Matrice 30, or Matrice 350 RTK.
- Payload options: Thermal cameras (e.g., DJI Zenmuse H20T) for moisture or insulation inspections.
- Battery & firmware checks: Ensure full charge and update firmware/software.
- Camera settings: Adjust ISO, shutter speed, and resolution for optimal clarity.
Flight Planning & Mission Setup
- Automated flight path: Use waypoints to ensure full coverage and repeatability.
- Manual flight for details: Inspect specific areas with potential damage manually.
- GPS & RTK setup: For improved georeferencing and accurate measurements.
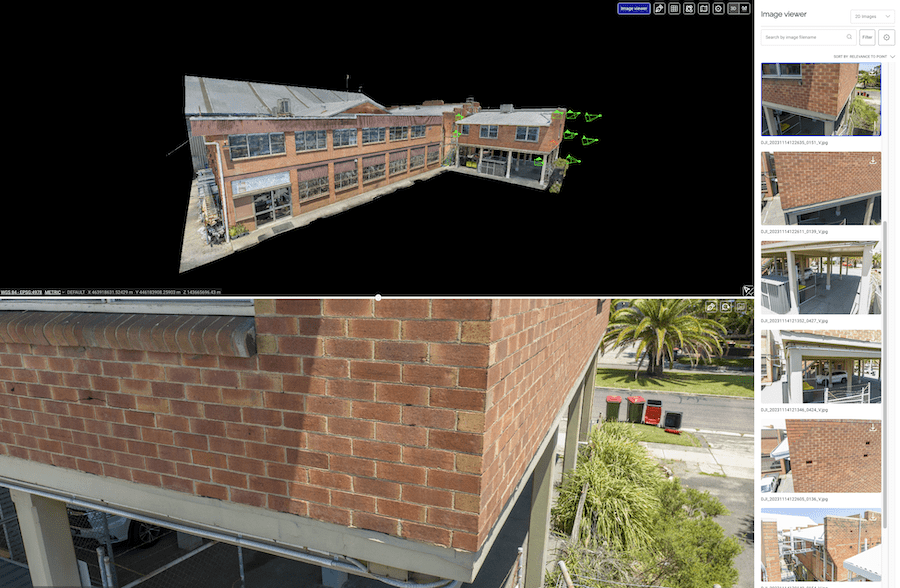
Methodology for Inspections
Data Collection Approaches
- Automated Grid Mapping – Ideal for 2D orthomosaics and 3D modeling.
- Waypoint Mission – Predefined paths ensure consistent data capture.
- Manual Visual Inspection – Focused on specific defects like cracks or missing materials.
Types of Data Captured
- RGB Images – High-resolution images for visual analysis.
- Thermal Imaging – Detects moisture or insulation issues.
- LiDAR Scans – Captures highly accurate 3D point clouds (if required).
Safety Priorities
- Regulatory Compliance – Follow local drone laws and airspace regulations.
- Operational Safety
- Avoid close proximity to people or traffic.
- Conduct pre-flight safety briefings.
- Monitor wind speed and weather conditions.
- Emergency Procedures
- Establish a fail-safe return-to-home (RTH) function.
- Have a backup pilot or observer for safety.
Deliverables & Software for Data Processing
Types of Deliverables
2D Orthomosaics
- High-resolution stitched image providing a top-down view.
- Used for measuring roof dimensions, damage locations.
- Pros: High detail, easy to analyze.
- Cons: Limited depth perception, not ideal for facade inspections.
3D Models & Point Clouds
- Full 3D representation of the structure for in-depth analysis.
- Ideal for facade and complex roof structures.
- Pros: Realistic visualization, accurate measurements.
- Cons: Requires powerful software, longer processing time.
Thermal Maps
- Identifies heat loss, leaks, or insulation gaps.
- Pros: Critical for energy audits.
- Cons: Requires specialized interpretation.
Inspection Reports
- Annotated images and defect localization for repair planning.
- Pros: Simplifies communication with maintenance teams.
Software Used for Processing
- Global Mapper, ArcGIS, Civil 3D – Powerful desktop GIS software for advanced geospatial analysis
- Agisoft Metashape, DJI Terra, Bentley Context Capture and Reality Capture – Advanced photogrammetry software for 3D modeling and ortho creation.
- Drone Deploy, Pix4D, Propeller Aero & Virtual Surveyor – Cloud-based processing and reports with 2D & 3D visualization providing high-accuracy geospatial analysis.
Context & Reference for Issue Identification
Some methods improve defect referencing by embedding GPS data and location markers into images, making it easier for teams to find and repair affected areas:
- Geo-tagged Images – Ensures precise defect localization.
- Augmented Reality (AR) Integration – Overlays defects onto the real-world view.
- AI-Powered Defect Detection – Automatically highlights cracks, corrosion, or missing materials.
By using a combination of automated flight paths, high-resolution imaging, and AI-driven software, drone inspections provide a safer, faster, and more cost-effective alternative to traditional building assessments.
