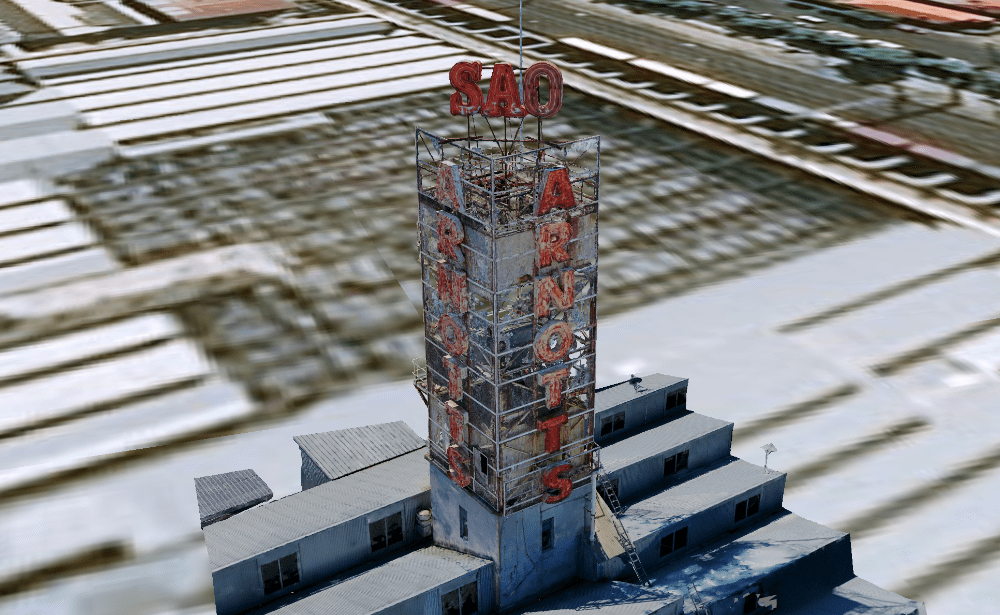
Brief:
The Arnott’s Factory at North Strathfield has been an iconic building in Sydney for over 100 years. Those driving passed in the 1990’s may remember the flashing neon Arnott’s Sao sign and delicious smell of baking biscuits. The SAO sign was erected on a tower on top of the factory over the past few decades has seen signs of heavy corrosion and deterioration.
The property owner was looking to either restore the SAO tower to its original state or potentially have it removed. A thorough inspection was required to determine the extent of the damage.
Solution:
The tower is accessible by ladder although the structure is not deemed safe currently due to the heavy corrosion. Therefore the client engaged High Exposure to provide a detailed aerial façade inspection of the structure. The engineering firm responsible was interested in 3D modelling capabilities having received a demonstration from High Exposure the month prior and thought this would be a perfect fit for their clients project.
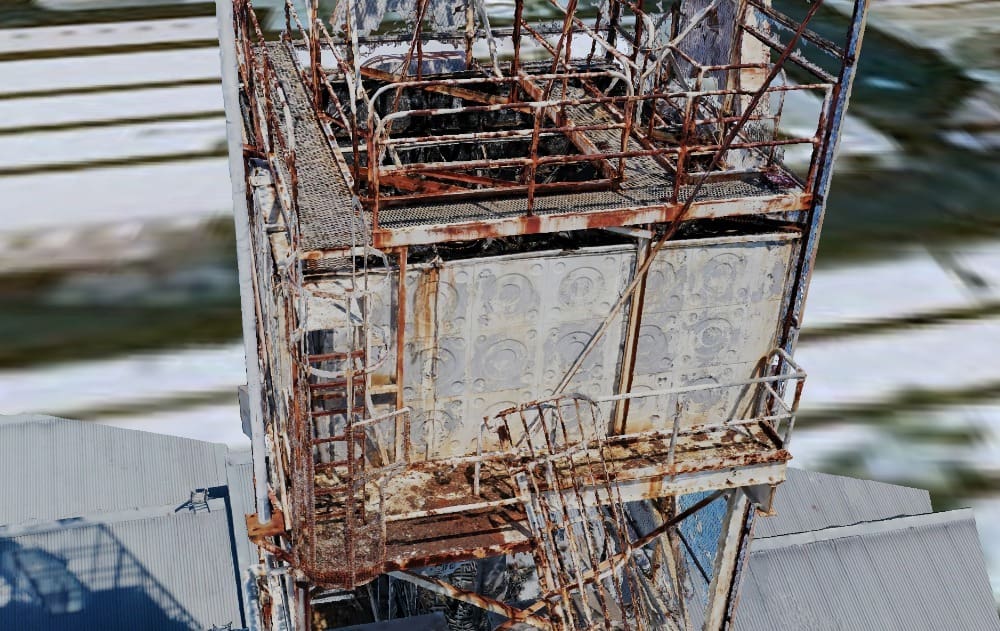
Method:
High Exposure has perfected the photogrammetry process over years to enable highly detailed models that are capable of remotely inspecting infrastructure to make informed decisions on next steps. A mapping drone capable of detailed images was utilised to capture the structure in half a day. The imagery is then processed using Bentley which is best in class 3D reality capture software. We then upload the model to Trendspek reporting visualisation software.
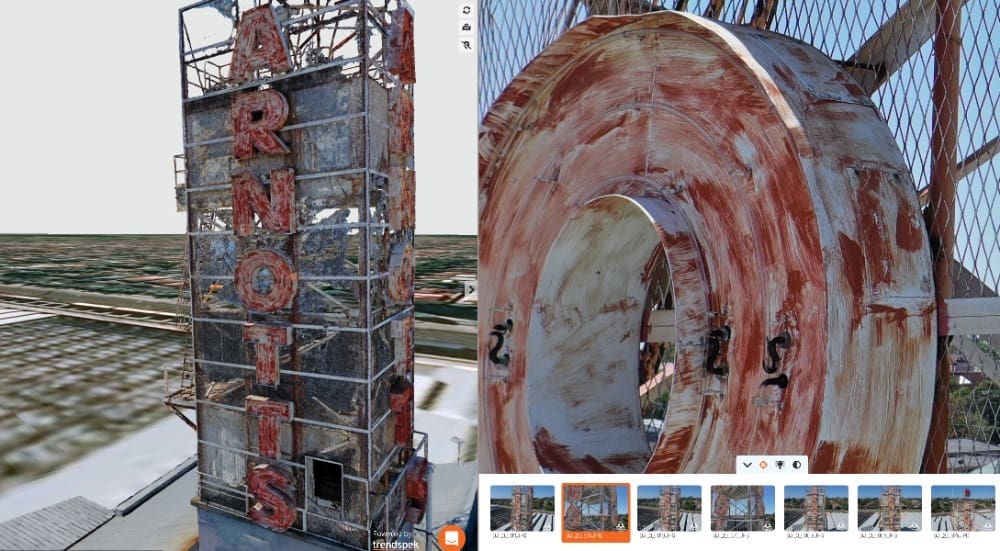
Outcome:
The 3D model provided a digital record showing great detail of all the corrosive elements of the structure and areas of interest may be in need of remedial work. This can be inspected by assessors in the comfort of their office. It is possible to take measurements on any area within the model as well as mark defect annotations that can be exported into a PDF report. The client was able to receive a phenomenal amount of data on the structure and report the findings in a way that until now was provided in a subjective format with gaps in data due to the non-comprehensive capture and defect identification method. Above all the data was provided with no risk to humans due to the drone able to access any point on the structure for ideal capture angles.